After years of being hammered by globalization and other economic factors, American manufacturing is finally making a comeback. Yet even with the upsides of increasing government and private sector investment, manufacturers are grappling with a skills gap that has the potential to cripple any positive momentum.
According to a study by Deloitte and The Manufacturing Institute, the on-going skills gap could result in 2.1 million unfilled jobs by 2030, culminating in a potential industry loss of up to $1 trillion in 2030 alone. According to survey respondents, finding the right talent is now 36% harder than it was in 2018, and executives report difficulties filling both higher paying entry-level production positions as well as recruiting and retaining skilled workers for specialized roles. Seventy-seven percent of manufacturers interviewed expect to have difficulties attracting and maintaining a workforce equipped with in-demand skills going forward.
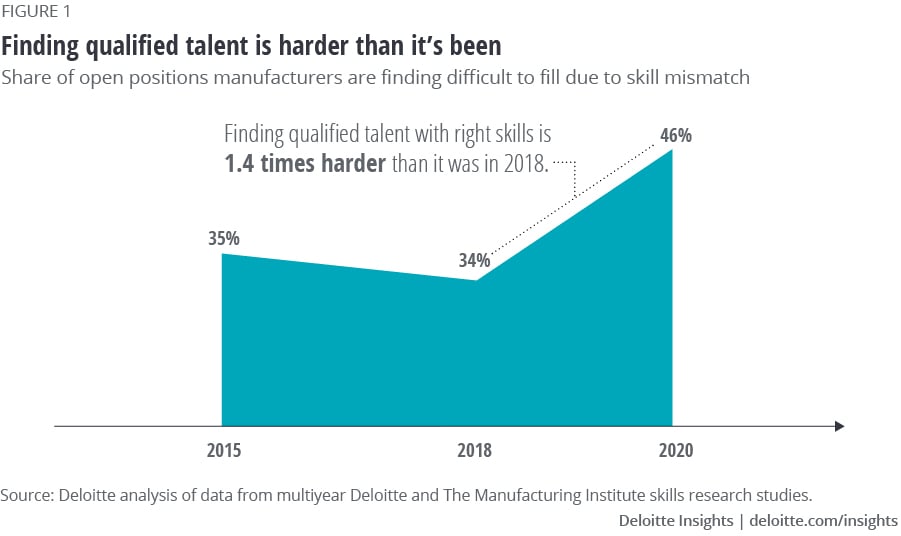
A surge in baby boomer retirements is making things worse. A Gallup poll put the average retirement age at 66 years old, with estimates that 2.6 million baby boomers will retire from manufacturing jobs over the next decade.
In theory, millennial and Gen Z candidates are a rich pool to draw from to fill in the gaps. To that point, the 2021 Future Manufacturing Workforce Study found attracting Gen Z talent to be a high priority for 88% of manufacturers surveyed. Yet despite the urgency, the same survey found 60% of respondents having challenges attracting Gen Z candidates to current positions, and 48% said they struggled to retain younger talent.
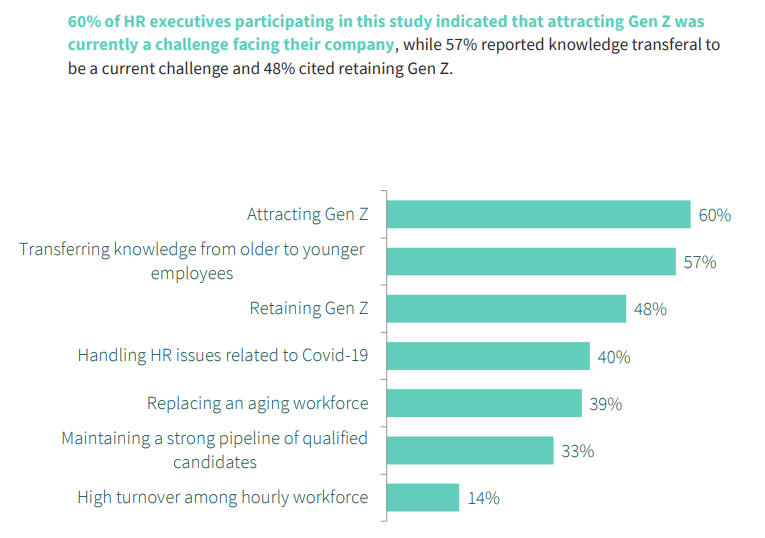
A lot of the issue lies with the perception among younger employees that manufacturing jobs are legacy, dependent on outdated tools and laborious manual processes. Younger employees, most born and raised as digital natives, don’t see value in joining a work environment and culture that doesn't offer the caliber of productivity and online experiences they’ve become accustomed to in their personal interactions.
One way around the problem is for manufacturers to embrace modern toolsets to transform the nature of automation work—a plus for a digital-savvy workforce committed to staying on the cutting-edge. A survey by Parsable found Gen Z expects employers to provide and utilize technology to help them advance their digital skills (18%).
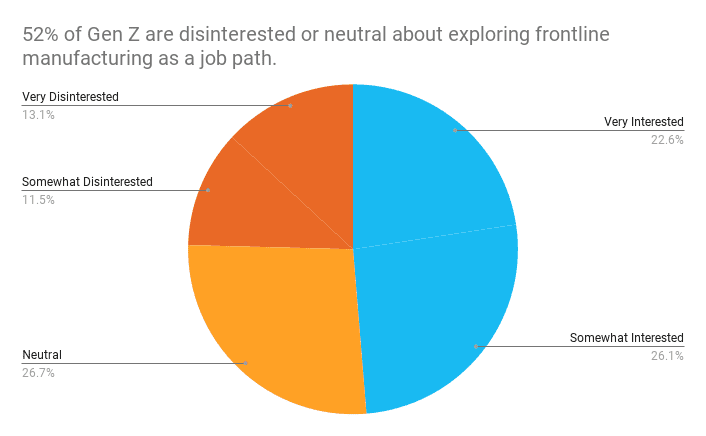
The Copia Git-based version control platform falls right into this category. The tool suite, which brings modern DevOps and a Git environment to PLC and controls programming, appeals to a younger generation of employees already acquainted with modern IT software development practices and who prioritize having a marketable skill set.
Compared to traditional PLC and controls tools which are hard to learn and only transferrable to a single vendor’s siloed platform, the Copia version control suite brings a modern and vendor-agnostic paradigm to PLC programming, facilitating collaboration and providing visibility into code changes. Gen Z candidates seeped in mainstream programming practices like automation, rapid feedback, and faster release cycles will feel right at home in the Copia platform. In comparison, traditional control system IDEs, which require specialized knowledge of specific vendor programming languages and a high degree of dependance on manual processes and experts, are likely to feel esoteric and unfamiliar.
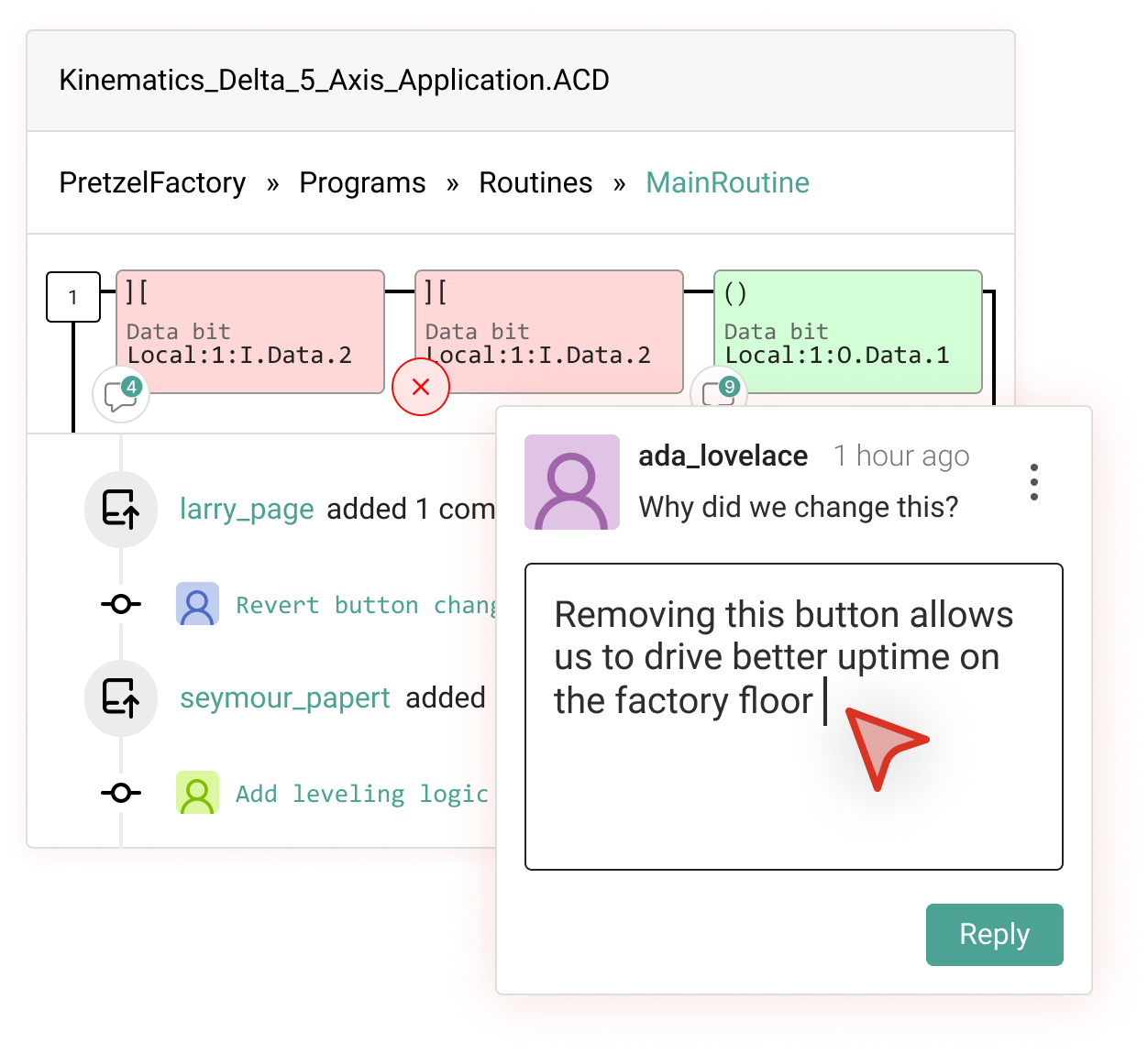
One engineering consulting firm was able to leverage the Copia platform to more quickly onboard new talent, particularly junior software engineers that typically require time with experienced mentors to learn the visual ladder logic diagrams required for PLC programming. Copia’s Git branching and merging capabilities, coupled with easy-to-read, color-coded comparisons for visualizing changes, sped up the feedback loop between the junior and senior engineers, saving review time and mitigating programming mistakes, officials there said.
A modern environment is certainly not the cure-all for manufacturers’ talent woes. Yet upleveling the experience can go a long way in demonstrating to up and coming engineers that automation is not a dead end, but rather a successful and rewarding career track.