I’ve rarely walked so much at a conference. The Orlando convention center is huge. After getting dropped by a Lyft at the wrong entrance on my second day, I walked three quarters of a mile (tracked by my Apple Watch) to get to my speaking session.
There was so much amazing technology, so many incredible companies, and thousands upon thousands of awesome, thoughtful people. When at a conference like this, I’m always saddened for the end because it always seems too short. The time goes by so fast as we get lost in the discussions – learning about different tech, exploring the art of the possible, debating the advancements and results that could be driven in the span of a year, before we meet again.
I appreciated the great opportunity to present three educational sessions while I was there:
1. Smart Manufacturing Bootcamp: Building a Competitive Advantage
2. Getting Started in Industrial Robotics Workshop
3. Limiting Risk and Improved Security for PLCs
People: The Real Source of Change
We had lively discussions and in all of these sessions, we focused on the best way to successfully use and adopt technology – through change management and a focus on the people behind the technology.
So often, technology is the focal point of change. Day after day, we see headlines and hear conversations about the importance of digital transformation – the need to bring in more and more technologies to gain a competitive edge in manufacturing, in distribution. What has typically come up short in these conversations is workforce. People are the catalysts of change and the drivers of technology. Without people, the technology will sit there, unused.
In my 'Smart Manufacturing Bootcamp,' we explored how companies can build a culture of continuous learning and provide employees with the skills they need to thrive in a digital environment. One attendee talked about training for their workforce, and another talked about mentorship to support culture and community within the evolution of their workplace. This collaborative approach minimized resistance to change and led to increased productivity and employee satisfaction.

IT / OT Convergence and Cybersecurity
Another key theme at FABTECH and every other conference I’ve attended this year was the increasing convergence of IT and OT (Operational Technology). This was particularly relevant during my session on 'Limiting Risk and Improved Security for PLCs,' where we discussed the growing importance of cybersecurity in manufacturing. With the rise of connected devices and the Industrial Internet of Things (IIoT), protecting critical infrastructure from cyberattacks is more crucial than ever, and more challenging. We talked about Shadow OT creating vulnerabilities that go unnoticed and undetected as employees look to get things done by adding and accessing technologies that will support their pursuit, despite the fact that their efforts widen the cyberattack surface.
This convergence also underscores the need for Industrial DevOps practices. By adopting principles like version control and automated backups, manufacturers can empower their workforce to better manage code changes, track modifications, and quickly recover from unexpected disruptions or cyberattacks. Imagine being able to instantly revert to a previous secure configuration in case of a breach – that's the power of effective DevOps in an increasingly interconnected industrial landscape. This capability also drives a culture of experimentation because people can try things without the fear of causing a shutdown or major disruption. This not only strengthens cybersecurity posture but also improves operational efficiency and agility, enabling faster responses to production demands and market changes.
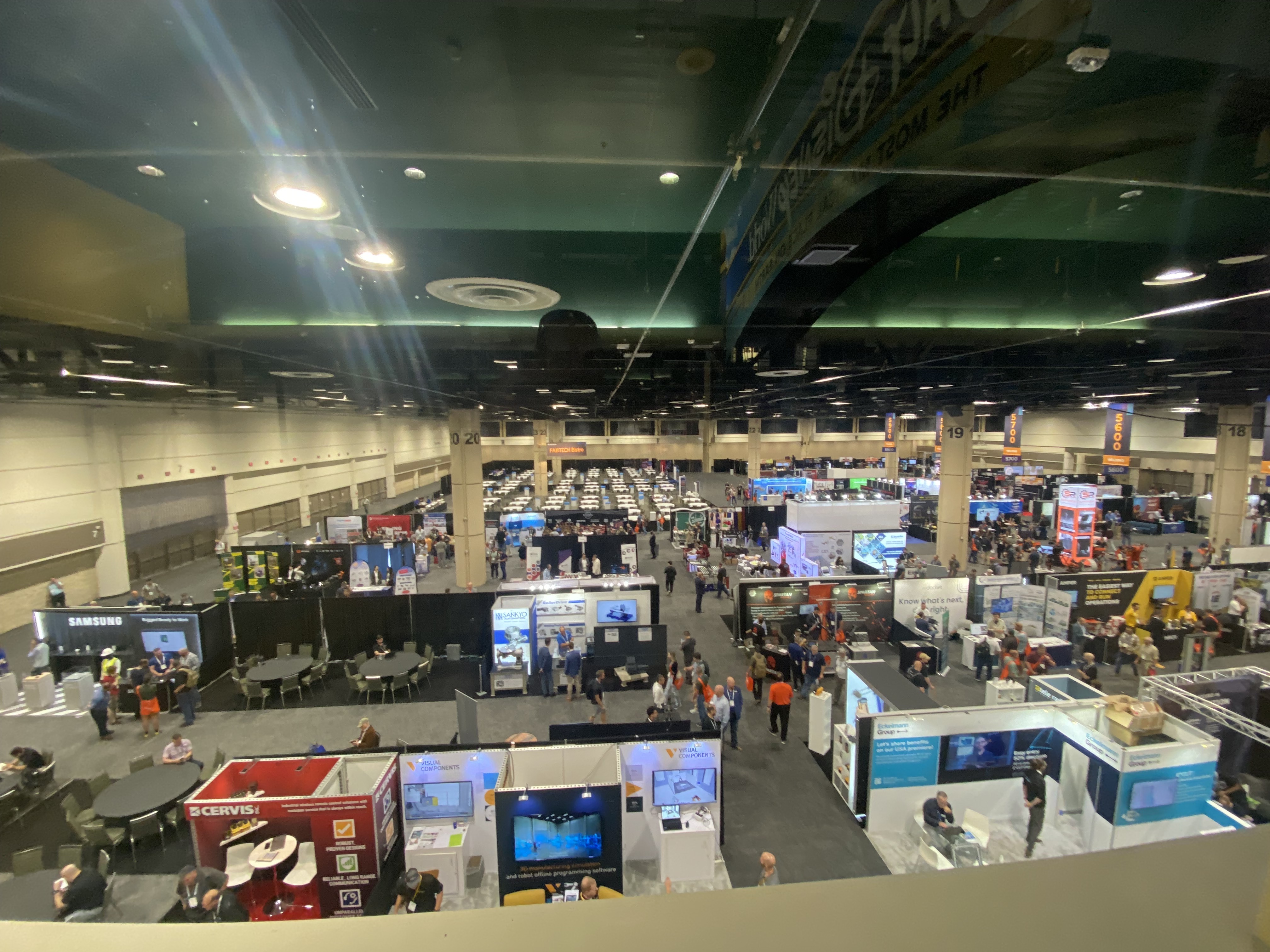
The Future of Manufacturing and Distribution
Ultimately, FABTECH reinforced my belief that the future of manufacturing is not just about adopting the latest technologies, but about empowering the people who use them. Technology is great. It took me from my hotel and dropped me off at my event, and it allowed me to connect with and pay that driver through an app – no need for cash, check, or credit. Technology also helped me track how far I had to walk to get to my session, which I appreciate because I like tracking my steps and hitting my number – 10k a day.
But at the core of tech, there are people. People who develop the apps that deliver the above results. People that participate in the execution of that technology’s mission on either end of the app. Without people, technology doesn’t do a whole lot. With people, technology can go awry, like how I selected my drop off point, but it was the wrong spot unbeknownst to me. Technology can only take you so far, and the human element remains crucial to driving digital success.
Of all the things I learned at FABTECH, the reinforcement of this idea is the most important: recognizing that technology is only a tool, and its true potential can only be unlocked by the ingenuity and dedication of the human workforce. What technologies we adopt and how we support that workforce in using them is the key to unlocking organizational potential and a competitive edge.
Looking for the right technology for your organization? Check out the first ever State of Industrial DevOps Report. This report provides an overview of where the industry is headed, and how Industrial DevOps can help you best be prepared to tackle the key challenges facing industrials and distribution.